As the wave of prefabrication sweeps the world, the "excessive strength and insufficient toughness" of precast concrete (PC) components has always been a pain point in the industry. The emergence of carbon fiber, the "black magician", is making beams, plates and columns evolve from "fragile sharks" to "seismic iron men".
Pain point: Why can't traditional PC components "hold up"?
Brittle failure: Ordinary concrete is resistant to compression but not tension, and it is easy to break instantly when bent or impacted.
Steel bar corrosion: Chloride ion erosion in coastal areas or chemical plants has caused the "internal injuries" of traditional steel bars to increase.
Weight shackles: Increasing the cross-section to increase the bearing capacity will increase the transportation and lifting costs.
Post-earthquake repair is difficult: Once the node area is cracked, the on-site wet operation repair cycle is long, delaying the resumption of work.
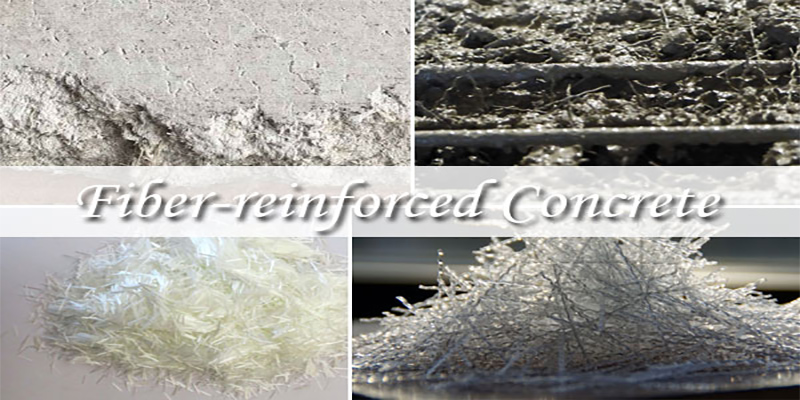
Four disruptive roles of carbon fiber
Internal addition of "short fiber" - "ligament reconstruction" for concrete
• Mechanism: 0.2%-0.8% volume addition of short-cut carbon fiber forms three-dimensional random support in the matrix. When cracks appear, the fiber "bridges" to transfer stress, and the impact toughness is increased by 2-4 times.
• Scenario: Prefabricated stairs, subway pipe segments, anti-collision guardrails and other components that need to be impact-resistant.
• Data: Prefabricated beams with 0.4% carbon fiber added have a 35% reduction in mid-span deflection and a 50% reduction in crack width in the drop hammer test.
External "CFRP cloth" - "invisible armor" with 10 times the strength of steel bars
• Mechanism: CFRP cloth with a tensile strength of ≥3000 MPa is glued to the tensile surface of the component with epoxy glue to form a secondary force system, which can increase the bending bearing capacity by 30%-50% without increasing the cross section.
• Scenarios:
– Rapid reinforcement of old prefabricated hollow slabs;
– Seismic upgrade of prefabricated bridges (such as CFRP cloth wrapped around the plastic hinge area of piers).
• Case: After two layers of CFRP cloth were attached to the bottom of the prefabricated box girder of a certain overpass, the ultimate bearing capacity was restored to 1.45 times the original design.
Prefabricated "CFRP bars/grids" - "super steel bars" that never rust
• Mechanism: Using CFRP bars to replace traditional steel bars has a density of only 1/5 of that of steel, but a tensile strength of 10 times that of steel, and is resistant to chloride ion corrosion.
• Scenarios:
– Prefabricated exterior wall panels for coastal docks and LNG storage tanks;
– Prefabricated bridge panels that need to be protected from salt corrosion in high-altitude cold areas.
• Economical: The cost of the entire life cycle is reduced by 30%, eliminating the need for later anti-corrosion coating.
Intelligent "perception layer" - let the components have their own "health checkup"
• Mechanism: The evenly dispersed short carbon fibers make the resistivity of concrete change linearly with strain, realizing self-diagnosis of cracks.
• Scenarios:
– Prefabricated integrated pipe corridors, real-time monitoring of settlement;
– Prefabricated building exterior wall panels, rapid assessment of damage levels after an earthquake.
How much has the durability of prefabricated components improved after being "armored" with carbon fiber? We have obvious data comparisons, which are mainly reflected in two aspects;
1. Quantitative indicators of improved durability
Crack width: After CFRP cloth reinforcement, the crack expansion rate decreased by 60%-75%; after 120 dry-wet cycles, the stress intensity factor at the crack tip decreased by 50%.
Rebar corrosion: After CFRP bars/grids replaced steel bars, the chloride ion permeability coefficient decreased by one order of magnitude, and the steel bar corrosion rate was <0.01 mm/year.
Freeze-thaw cycle: After 300 rapid freeze-thaw (F-T) tests, the CFRP-concrete interface bond strength retention rate was ≥85%, while the unreinforced specimens only had 50%.
Ultraviolet aging: After continuous irradiation with UV-A 340 nm lamp for 1000 h, the tensile strength attenuation of CFRP cloth was <5%, which is much better than the 20% attenuation of epoxy-coated steel bars.
2. Environmental adaptability: Performance under extreme working conditions
High temperature and high humidity (40 ℃, RH 95%)
After 3000 h, the shear strength of the CFRP-concrete interface decreased by <8%, meeting the 30-year equivalent requirements of JTG/T J22-2011 for hot and humid environments.
Salt spray + dry-wet cycle (NaCl 5%, 120 cycles)
The bond strength of traditional reinforced concrete decayed by 50%, while the CFRP reinforced specimen only decayed by 12%.
Freeze-thaw + deicing salt (-18 ℃↗+5 ℃, 300 cycles)
The ultimate load of the CFRP cloth specimen decreased by <10%, while that of ordinary concrete decreased by 35%.
Therefore, carbon fiber is not simply "more expensive steel bars", but the key to the evolution of precast concrete from "passive load-bearing" to "active sensing". Whoever masters this key first will be able to open up a high value-added blue ocean in the red ocean of prefabricated buildings.