In the world of precast concrete components, lifting anchors are the lifeline connecting the components to the lifting equipment. A single incorrect installation can cause components to slip, damage equipment, or even result in fatalities. Safely installing lifting anchors is no small matter; it's a paramount concern for both production efficiency and personal safety.
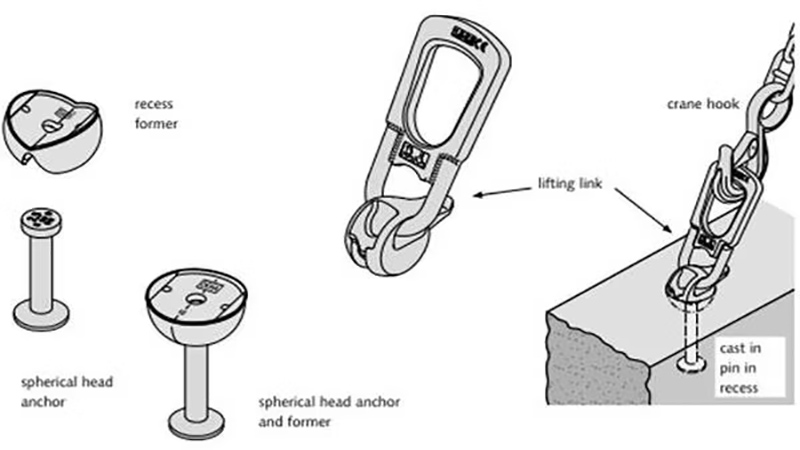
Lifting Anchors: The "Life Hook" of Precast Components
Lifting anchors are embedded in concrete components and serve as the core load-bearing point for connecting slings to facilitate lifting, tilting, and transportation. They determine the "lifeline" of the component from the production line to the installation site. Therefore, they are an essential component in precast concrete. Common types include:
Internally Threaded: Threaded holes are pre-recorded in the component surface for eyebolt installation.
Externally Threaded: An anchor with external threads is embedded in the component surface for eyenut installation.
Embedded Eyebolt: The eyebolt is embedded directly into the component.
Step-by-Step Installation Guide
Pre-Installation Checklist
Before installing lifting anchors in precast concrete, proper preparation is key to ensuring structural safety and efficient lifting. Here's your essential checklist:
Review Construction Drawings and Specifications
: Carefully review all technical drawings, lifting plans, and anchor specifications. Identify the required anchor type, location, and load rating to prevent conflicts or delays on site.
Choose the correct anchor point location and spacing: Anchor point placement must align with the panel's center of gravity and lifting direction. Incorrect spacing can cause tilting, rotation, or even panel failure during lifting.
Prepare Materials in Advance: Gather all required components: lifting anchors, groove formers, rebar templates, and sleeves. Ensure compatibility and quality compliance.
Gather Required Tools:
Use precision tools such as a laser rangefinder and level. Don't forget safety gear (helmet, gloves, vest) and installation aids such as fixing clamps or spacers.
Safety Red Lines and Key Considerations
Bearing capacity is the bottom line: Overloading is strictly prohibited! Anchors and matching rigging must be designed with the specified bearing capacity.
Thread protection is vital: The cleanliness and integrity of internal and external threads directly determine the strength of the connection. Never allow exposed threads to become damaged or clogged!
Shifting is a major risk: The anchor must be securely positioned during pouring and vibration. Any shifting can result in uneven load during lifting or even failure.
Concrete density is a guarantee: Weak concrete around the anchor can significantly weaken the anchoring force and pose a major safety hazard.
Regular inspection and maintenance: Reusable embedded sleeves, anchor plates, fixing brackets, etc. must be regularly inspected for wear and deformation and replaced promptly. Eyebolts/nuts should be regularly inspected for thread and load conditions.
Final confirmation before use: Before lifting, a dedicated person must re-check:
Anchor type and location are consistent with the drawings.
Threads are clean and intact, and the connectors (eyebolts/nuts) are correctly installed and tightened to the specified torque. The lifting rings are free of deformation and cracks.
The surrounding concrete is free of cracks, chipping, or other defects.