Under the wave of building industrialization, the production efficiency and precision of precast concrete components directly determine the quality and cost of the project. Traditional wooden and steel molds rely on manual positioning and bolt fixing, which often lead to component size errors due to installation deviations, template deformation and other problems. Especially in mass production, the accumulation of small errors may trigger a chain reaction. The magnetic formwork system is becoming a key technology to solve this pain point through innovative design.
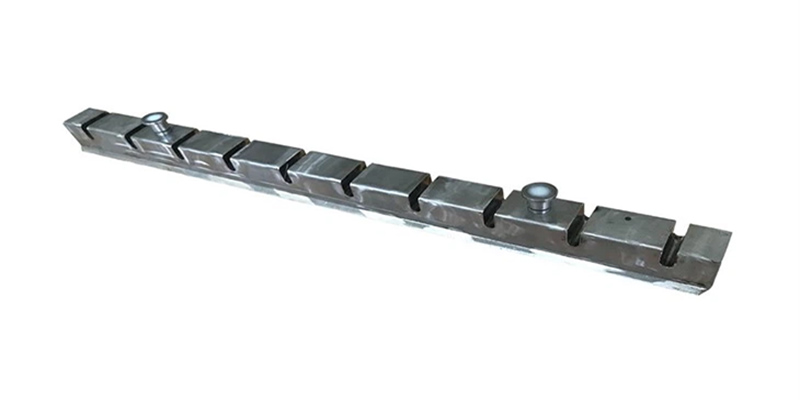
So what is a magnetic formwork system?
It is an innovative technology that uses magnetic force to fix and position the formwork. It uses devices such as magnetic boxes or electromagnetic clamps to firmly adsorb the formwork on the steel bottom formwork or other supporting structures, thereby realizing the rapid installation and removal of the formwork. This system not only improves construction efficiency, but also significantly improves the production accuracy of precast concrete components through precise magnetic control.
The pain of traditional formwork is that it causes the precision out of control and efficiency bottleneck of the project.
Traditional precast concrete formwork faces three major challenges:
1. High dependence on labor: Bolt tightening and support calibration rely on workers' experience, which is easy to introduce human errors;
2. Low repetition accuracy: When the formwork is disassembled and reassembled, the positioning consistency is difficult to ensure;
3. High risk of deformation: Concrete pouring pressure may cause local displacement of the formwork and affect the forming size.
These problems are particularly prominent in large-scale production. According to statistics, the rework rate under traditional processes can reach 5%-8%, and the size fluctuation of each batch of components often exceeds ±3mm, affecting the subsequent assembly efficiency.
The magnetic formwork system reconstructs the formwork fixing logic through magnetic adsorption technology and modular design:
- Precise positioning: The electromagnetic device is built into the template joint, which generates strong magnetic closure after power-on, achieving seamless docking and eliminating the deviation caused by the gap of traditional bolt holes (accuracy control up to ±0.5mm);
- Rigid reinforcement: The magnetic field is evenly distributed, which increases the overall compressive strength of the formwork by more than 30% and resists the side pressure deformation of the concrete;
- Intelligent control: The sensor is used to monitor the state of the formwork in real time, and the abnormal displacement automatically alarms to prevent the production of batch defective products.
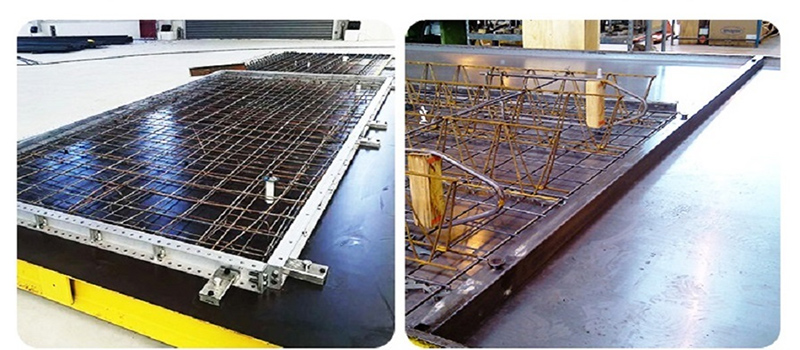
How to achieve "zero rework" production? There are three advantages to analyze
1. Dimension deviation control: a leap from centimeters to millimeters
The magnetic adsorption force ensures that the template is tightly spliced, avoiding the dislocation caused by loose bolts or welding deformation in traditional processes. Taking a prefabricated wall panel production line as an example, after using the magnetic template, the length deviation is reduced from ±3mm to ±0.8mm, and the qualified rate is increased to 99.6%.
2. Component consistency: the secret of standardized replication
Modular magnetic templates support fast disassembly and resetting. Through the preset magnetic pole encoding, the template is automatically aligned each time it is reorganized to ensure that the dimensions of thousands of components are highly uniform. This is crucial to the "interchangeability" requirements in prefabricated buildings.
3. Reduced rework rate: dual savings in cost and time
High precision directly reduces the need for secondary processing such as repair and cutting.
Why is it designed for "mass production"?
1. Extremely fast mold change: Traditional template change takes several hours, and the magnetic module can switch to a new component mold within 20 minutes through combination adjustment;
2. Life and reusability: The high-strength magnetic material has a life of more than 100,000 times, suitable for long-term repeated use;
3. Compatible with automation: Seamless docking with robotic arms and casting robots to achieve full-process digital control, suitable for the expansion needs of smart factories.